Complete Copper and Brass Manufacturing Plant
For Sale
ROD AND BAR PLANT FOR BRASS AND COPPER (8190)
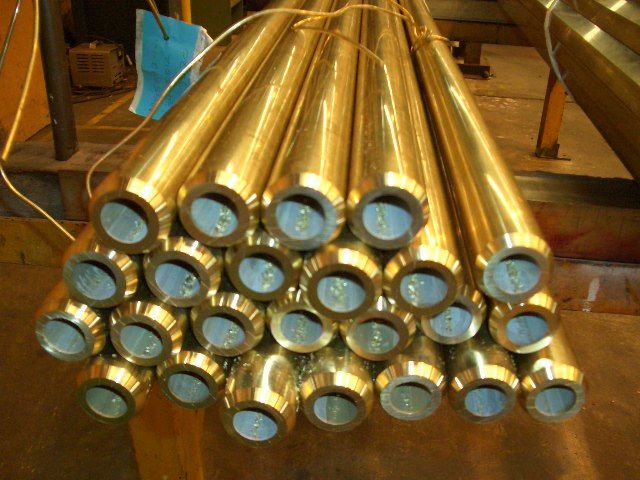
Click on picture below for larger version
Lockwood & Co are pleased to offer for sale one of the world's premier factories
for the production of brass and copper rod, bar, shapes, hollows, bus bar and
anode ball. The plant is being offered in its entirety or in major sections
only and is not for sale on an individual machine basis. It can be seen in operation
through to the end of 2005. The Consolidated Extrusions Pty. Ltd. plant was
constructed in 1990 as a combination of three other plants. In addition a large
amount of new equipment was added at this time. The plant has a capability of
over 30,000 tons per annum and produces an exceptionally wide range of solid
and hollow copper and copper alloy product such as :
- Round, hexagon and octagon bars from 3.2 mm to 100 mm (1/8"-4")
- Flats from 6.35 to 152.3 ( 1/4"-6") x thickness from 1.6mm (.063")
- Hollows to 100mm (4") ID
- Copper bus bars from 12.7 X 3.2 to 200 x 12 mm (5"x 1/8" to 8"x 4-3/4")
- Near net shape extrusions in copper and brass
- Wire from 1.45mm (0.057") to 10mm (0.40) dia. in straight length & coil
- Straight length welding wires from 1.6mm to 6.4mm (.063"-0.25") dia.
- Seamless brass box sections
- Standard angles and channels from 12.7mm (5")
- Shaped brass extrusions for structural and decorative architectural purposes.
The plant is located in Australia, approximately 45 minutes drive from Sydney
Airport and is currently in full operation.
The plant is a fully integrated facility, comprising the following areas and
major plant items:
Melting and casting
- Two 2.5m W coreless melting furnaces & one 1m W channel melting furnace
- Two twin strand horizontal continuous casting machines for billet & log
- Twin strand semi-continuous caster
- Swarf drier and scrap sorting and handling equipment
- Baghouse for fume control from each furnace
Extrusion
- Three direct extrusion presses with piercers producing straight lengths
and coils including:
- 3000 Ton UBE Oil Hydraulic Press with 593 ton piercer, Junker Gas-fired
billet furnace (all new in 1984), straight runout w/walking beam cooling table
for straight lengths and dual coilers for rod coils, new PLC controls added
in 2001, double saw cutoff system added in 2004.
- 2050 Ton Schloemann Oil Hydraulic Press with 315 ton piercer, Granco Gas-
fired billet furnace, straight runout with walking beam cooling table for
straight lengths & dual coilers for rod coils, new PLC controls added in 1989,
new discard system added in 1997.
- 1600 Ton Schloemann Oil Hydraulic Press with 245 Ton piercer, Junker induction
billet furnace, automated log feeder with Oliver billet saw added in 1996.
Small rod area
- Fully automatic coil pickling system
- Five Schumag combined drawing lines for production of straight length rounds,
hexagons and squares to a maximum size of 29mm
- All lines feature in line cut to length and chamfering allowing direct on
line packing of product
Large rod area
- Rod pickling plant complete with electrolytic copper recovery cell.
- Three drawbenches complete with push pointing
- Kieserling automated straightening center comprising bundle loader, NC controlled
two roll reeler and cut to length & chamfering system
- Other straightening and sawing plant
- Bogie hearth annealing furnace
Copper bus bar area
- Large bar roller pointer
- Automated processing center comprising drawbench, straightener and cut to
length equipment.
- Coil fed drawbench with die head shear for small bars
- Copper flats pancake coiler
Flats processing
- Automated stretching and cut to length line for small flats
Wire area
- Triple draw, three head Koch draw block
- Two spinner type draw blocks
- Four vertical draw blocks
- RWF two stand wire flattening line complete with level winder
- Bogie hearth annealing furnace
Welding wire area
- Wire pickle area
- Breakdown block
- Showa triple block
- Finishing block
- Bogie hearth annealing furnace
- Six straighten & cut lines w/two including in-line draw blocks.
Section production area
- 75 Ton, 40 ton, 25 ton and 8 ton hydraulic stretch straighteners
- Three Seifer profile correction machines
- Two automated shorts cutting saws.
- Drawbench for box section production
- Behringer band saw for bundling cutting of sections
- Finishing machine for flats
Die design and manufacture area - features
- Die design via Autocad and .... CNC interface
- Five high output CNC wire cut machines
- CNC Carbon electrode cutter
- Six die sinkers
- Two Okuma CNC lathes
- Two Okuma CNC machining centers
- Fluidized bed heat treatment facility
- ExtrudeHone die polishing machines
Warehouse area
- High bay cantilever racking system
- Three narrow aisle four directional forklifts
Laboratory area (Third party accredited)
- One XRF Spectrograph for metal analysis
- One ICP Spectrometer
- Physical testing equipment including hardness and tensile testing equipment
Maintenance and spare parts area
- Lathes, mills, welding equipment, press & normal maintenance equipment
- Comprehensive maintenance store
Tooling
- Die library of extrusion, drawing, straightening & section correction tooling
covering over 4000 individual products.
For Further Details Please Contact:
Mr. Tom Lockwood - Managing Director, Lockwood
& Co Pty Ltd
Tel: 61 3 9338 2778
Mobile: 61 419 310 852
Email: toml@lockwoodcompany.com.au
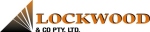